The Aluminum Advantage in Automotive Design
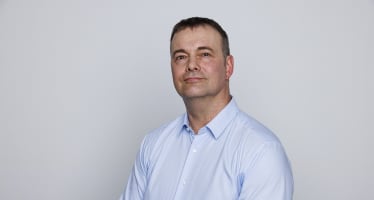
Andreas Afseth, Technical Director for Global Automotive & Specialties
BACK TO ALUMINUM EXPERT SERIES
Since the 1970s, there has been a steady increase in the quantity of aluminum used in car components, from engines, transmission cases, heat exchangers, and wheels, to hoods, doors, and crash management systems, to full aluminum bodies. Now we are seeing a new wave of increase in aluminum content per vehicle, as powertrains shift from internal combustion engines (ICE) to battery electric vehicles (BEVs). In almost every case, OEM engineers’ decision to choose aluminum over other materials is for affordable and sustainable lightweighting.
ALUMINUM WEIGHS LESS
Henry Ford used to say “excess weight kills any self-propelled vehicle.” Mass has a huge impact on performance and energy consumption, affecting how well a car handles, how long it takes to brake, and the energy it uses to drive.
Today, the reference material for car body construction is steel. Steel of any grade weighs about 7.8 kg per liter of volume, while automotive grade aluminum alloys weigh around 2.7 kg per liter. When we compare any car body or component designed in equally optimized steel or aluminum grades with the same structural strength, stiffness, and performance, the aluminum part will typically weigh 40% less than the steel reference. This lightweighting value of 40% is not a constant, and depends on a part’s design limitations, but in general if you remove 100 kg of steel in a car body you can be fairly certain that 60 kg of aluminum will replace it.
Furthermore, lightweighting a vehicle body leads to secondary mass savings, or downsizing of many of the car’s other parts. You can have the same crash performance, acceleration, top speed, or range with less powerful motors or engine, less batteries, smaller brakes, lighter chassis and suspension, lighter wheels and tires.
LIGHTWEIGHTING CREATES AFFORDABILITY
When considering materials selection and cost, automotive engineers often talk about the cost-per-kg-saved. For BEVs specifically, the batteries are still the most expensive part of the car—and reducing weight in the body structure or closures means a vehicle requires fewer battery cells, smaller electric motors, etc., to meet overall performance targets. So, while aluminum as a raw material for car body construction is somewhat more expensive than steel both in term of cost per kg and cost per individual part, the overall vehicle cost can be identical or even lower for an aluminum intensive design compared to a steel intensive one.
A recent Alumobility study demonstrated that when converting a steel-intensive battery electric delivery vehicle to an aluminum design, it was possible to replace 870 kg of steel in the body and closures with 460 kg of aluminum (a 47% weight save). The material and manufacturing cost of the aluminum parts, at €2,500, was almost twice as high as that of steel at €1,300, but this difference was more than compensated by the savings from a 6 kWh smaller battery, 10 kW smaller motor, and reduced chassis, suspension, and wheels. Ultimately, the lightweight, aluminum-intensive delivery van with better payload and energy efficiency had a lower manufacturing cost than the steel reference.
Aluminum is relatively unique among materials in fitting this affordability criterium. Other materials might give more lightweighting, such as magnesium, titanium, or carbon fiber reinforced plastic composites (CFRP). But while a component made in CRFP may achieve a 70% weight saving compared to steel, it comes at a much higher cost of tens or even hundreds of euros per kg saved, making it non-competitive for all practical applications except very niche luxury or super sports cars.
ALUMINUM IS CIRCULAR
Faced with the challenges of climate change, the majority of automotive OEMs are committed to aggressive, short-term reduction in their carbon footprint, and to medium- to long-term net-zero status. A focus on materials suppliers and manufacturing phase sustainability is hugely accelerated by the transition from ICE to BEV, since the life cycle environmental impact of BEVs is dominated by the manufacturing phase, whereas that of ICEVs is mainly caused by the use phase and tailpipe emissions.
OEMs need materials that are circular (can be recycled again and again after the useful life of the vehicle) and produced in a way that does not emit greenhouse gases. Aluminum is infinitely recyclable, and can be sorted, remelted, and manufactured back into new cars without a loss in properties. The aluminum concentration in today’s end-of-life cars is relatively low and casting-rich, so the scrap is mainly used in secondary casting alloys. But with time, as newer cars with larger amounts of wrought alloy content reach their end of life, this scrap will become a key source for new automotive sheet and extrusion products.
Alternative lightweight materials such as glass fiber reinforced plastics (GFRP) or CFRP cannot (yet) be considered as circular, since it is not possible with today’s technology to recycle them multiple times. It may be possible to downcycle reinforced plastic composites into other end uses (roadbuilding, construction, etc.), but since that can only be done one time it does not represent circularity.
ALUMINUM’S FOOTPRINT IS COMPETITIVE
In the automotive industry, the term carbon footprint refers to how many kg of CO2eq emissions are released in the manufacturing phase of 1 kg of automotive raw material. In order for aluminum to maintain competitiveness with steel, and support OEMs in reaching their carbon footprint targets, we must match or be better on a part-by-part or full vehicle basis.
If steel suppliers can offer OEMs automotive grades with a carbon footprint of 2.3 kg CO2eqper kg today, and commit to a carbon footprint of 1.5 kg/kg by 2030, the part-by-part equivalent, considering a 40% lightweighting and secondary savings, means that an aluminum product needs to be below about 4 kg/kg today and below 2.5 kg/kg by 2030. The good news is that these targets are technically feasible, although ramping the volumes up to the necessary level will require big changes and investments.
As targets for both cost and carbon footprint continue to evolve, aluminum can help OEMs to achieve their goals through affordable and sustainable lightweighting.