Navigating the Road to Decarbonization
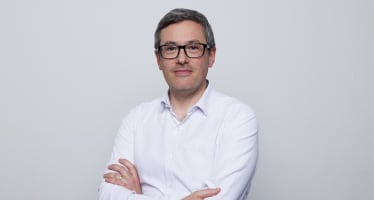
Fabien Mortier, Key Account Manager
The Paris Climate Agreement of 2015 ushered in a new wave of regulations and commitments to combat climate change, with the transportation sector—still responsible for 23% of global CO2eq emissions in 2022—squarely in focus. To meet their ambitious sustainability targets within the next few decades, automakers must adopt a multifaceted approach that goes beyond electrification, embracing circularity and the use of innovative, sustainable materials.
ROADMAPS TO DECARBONIZATION
Since COP21, more than 140 countries have set long-term net zero targets (2050 for the EU), as well as shorter term goals. Incentives for zero emissions vehicles will be followed by a phase-out of fossil fuel vehicles. A ban on ICE vehicle sales starts in 2025 in Norway; in 2035 in most other European countries, US, and China; and in 2040 in India.
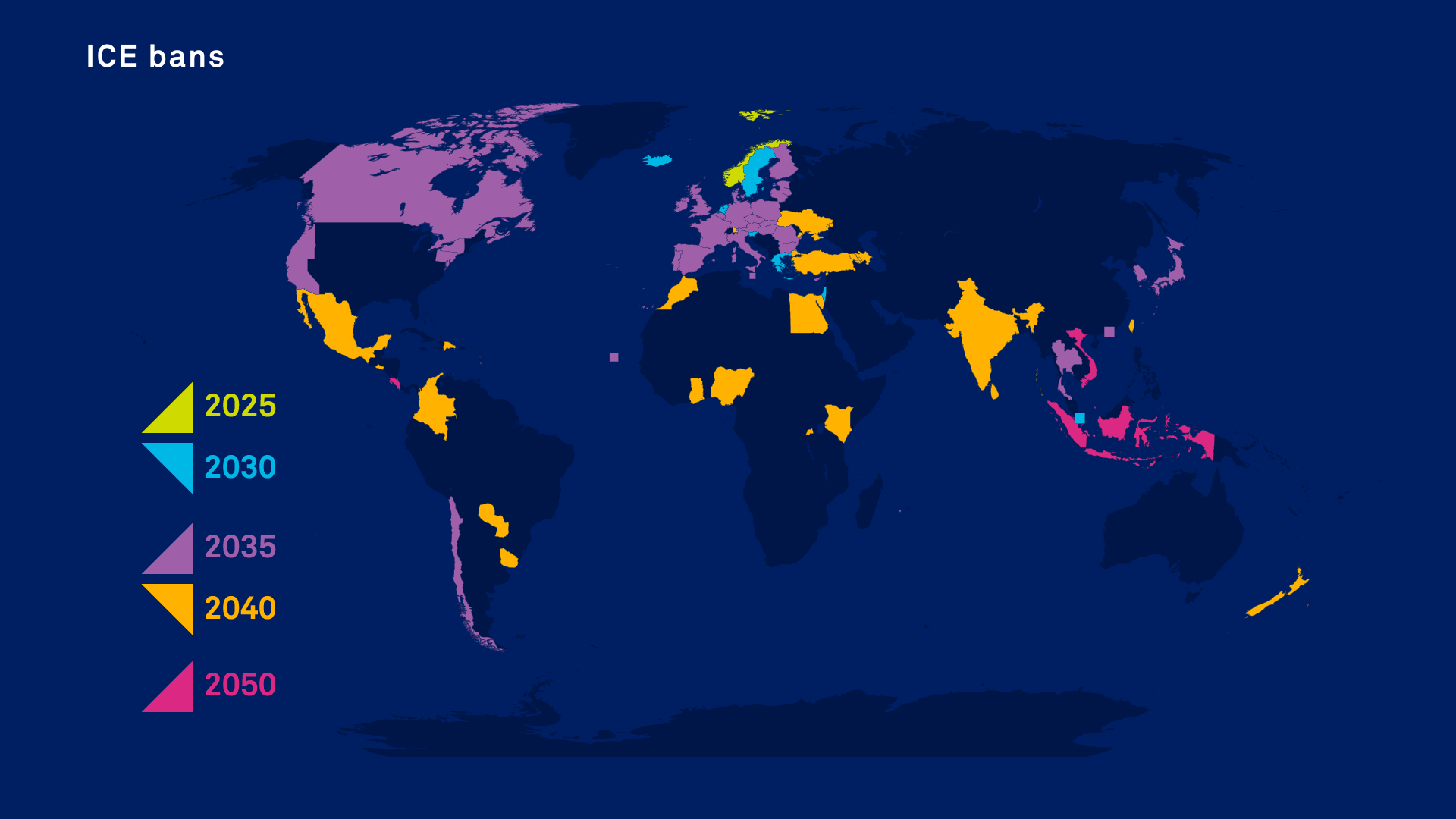
What may seem a vague and distant future for most of us is already becoming a reality for automotive OEMs. A typical automotive project has a development time of two to three years, and a life cycle of five to 10 years. Therefore, projects currently in the development phase must already consider the impact of regulations that take effect between 2030 and 2040.
Since 2020, all major OEMs have communicated about their strategies to reach carbon neutrality. While each has its own vision and roadmap, we can identify certain trends:
Electrification is the preferred way to achieve compliance with ICE bans and decarbonization in the use phase; e-fuels and hydrogen will be insignificant.
Decarbonization of the production phase starts with OEM plants’ direct emissions and continues with the upstream supply chain.
There is greater emphasis on sustainability throughout the supply chain and in raw material sourcing, with a particular focus on critical minerals.
New design models feature better disassembly and material recycling, and reused or recycled materials during manufacturing, for circular economy and resource conservation.
Higher ethical standards, with a focus on environment and social responsibility.
ELECTRIFICATION IS ONLY PART OF THE STORY
Life cycle assessments of similar ICE and BEV vehicles, from 2022 and 2030, shows that electrification drastically reduces CO2eq emissions in the use phase, but with slightly increased emissions during the production phase. It is insufficient alone for reaching carbon neutrality. Furthermore, the increased demand for bigger vehicles and SUVs is partly offsetting the progress made.
CO2eq emissions of different steps, in metric tons
Powertrain Year | Gasoline 2022 | BEV 2022 | Gasoline 2030 | BEV 2030 |
Use phase (incl. upstream) | 48.9 | 8.2 | 44.2 | 4.9 |
Vehicle Production | 6.7 | 6.0 | 4.1 | 3.6 |
Battery Production | 0.0 | 4.7 | 0.0 | 3.3 |
Recycling | -1.3 | -2.0 | -0.9 | -1.5 |
TOTAL | 54.3 | 16.8 | 47.4 | 10.3 |
(source: European NGO Transport & Environment – EU 27 average electricity grid)
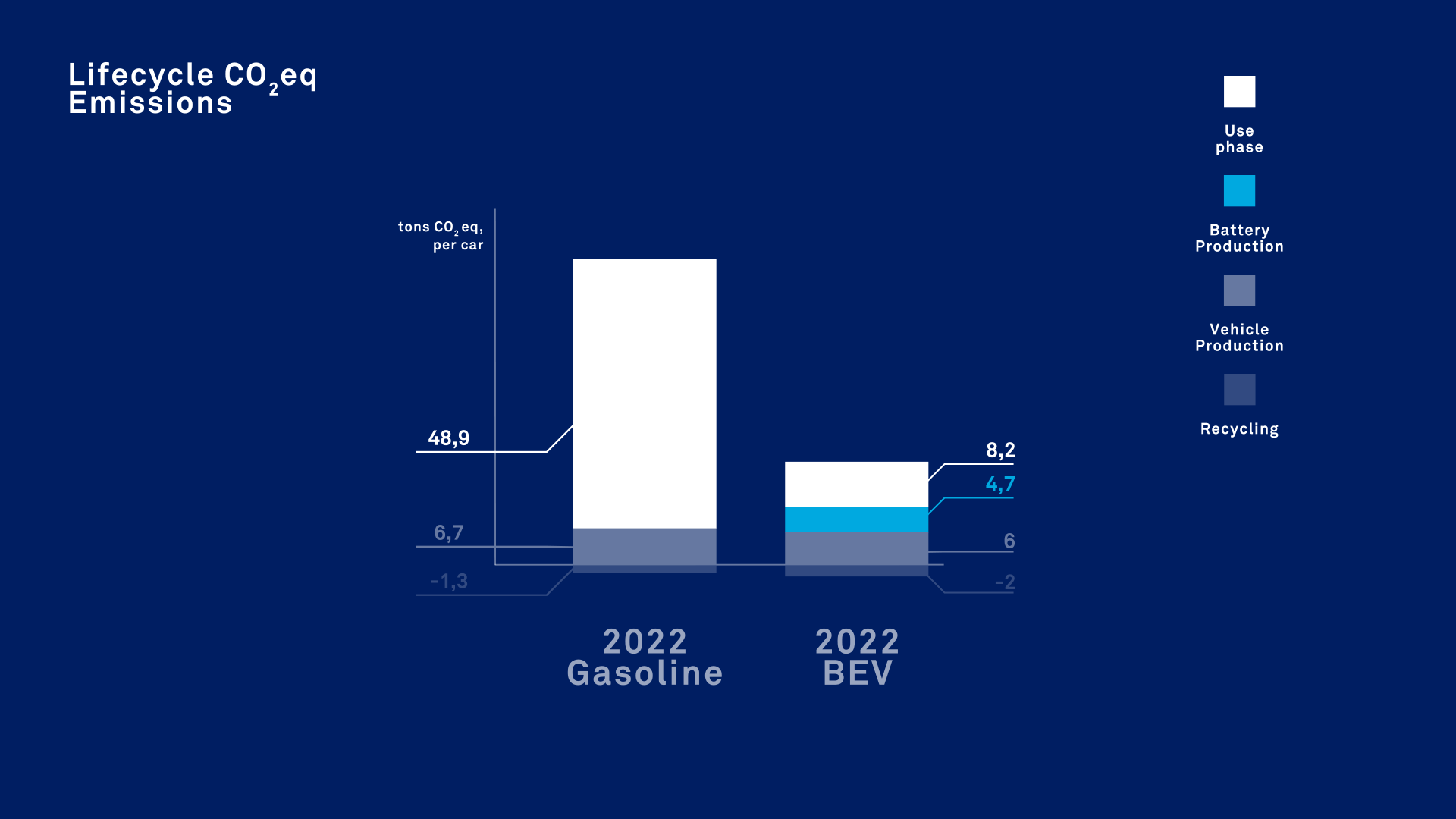
Carbon neutrality can only be achieved by tackling emissions related to the production phase as well. As for many industries, most of these are linked to the raw materials needed upstream (Scope 3).
CIRCULARITY SOLVES SEVERAL PROBLEMS
GHG emissions are only one of the stresses that human activities are putting on the environment. There are growing concerns about resource availability (particularly critical minerals), and about the environmental and social consequences of raw material extraction. The major OEMs have all defined targets for carbon footprint as well as resource preservation.
Circularity applied to materials such as steel and aluminum addresses both issues, though aluminum has certain advantages. When alloys are segregated and scrap collected, aluminum can be recycled and reused for the same applications without losing its properties. Improvement of alloys, material grades, and segregation processes will allow the use of new sources of scrap for automotive applications, which are considered unsuitable for such purposes today.
THE GREENEST ENERGY IS THE ENERGY NOT USED
Recycled aluminum uses 95% less energy than primary aluminum production, avoiding the use of electricity in the electrolysis process. This is an advantage even when compared to primary aluminum produced with low-carbon electricity, because each KWh of spared low carbon electricity can be used for other applications, replacing electricity produced with fossil sources. This point will remain key as long as low-carbon electricity production is insufficient to fully cover the needs of the electricity grid.
Despite promising growth in renewables, in 2022 power production remained the biggest contributor to GHG emissions, accounting for 42% of all emissions worldwide*.
* source: IEA report 2022
SUSTAINABILITY REDEFINES MATERIAL SELECTION
OEMs are choosing the most suitable material for each automotive part, looking at the best balance of weight, mechanical properties, cost…and now adding the carbon footprint of production to these criteria.
Aluminum has a historical competitive benefit by allowing for weight savings and decreased carbon emissions in the use phase. Considering the importance now given to carbon emissions during the production phase, lightweighting, though critical, is not enough.
Over time, the traditional criteria used by OEMs to evaluate materials have evolved beyond mechanical properties, lightweighting, and cost considerations. These factors, while important, are no longer sufficient in addressing the critical demands of sustainability and climate change.
At Constellium, we are committed to supporting automotive customers in achieving their sustainability goals through innovative low-carbon aluminum solutions. Our auto body sheets (ABS) can be tailored to include a guaranteed low carbon footprint, high recycled content, or primary aluminum produced using renewable energy—while maintaining the same properties, performance, durability, and recyclability as our standard offerings.
These low-carbon solutions are available across our full range of ABS products, encompassing inner, outer, and structural applications designed to meet the specifications of all major OEMs. Additionally, we can provide ASI-certified metal, ensuring the highest sustainability standards.
Our solutions are third-party verified, with transparent annual reporting and communication to support your sustainability commitments.