Blog post
Look around—there are more and more battery electric vehicles on the roads. And more aluminium, too.
By 2035, according to Goldman Sachs Research, battery electric vehicles (BEVs) will make up around half of new car sales worldwide. Much of that growth is driven by regulation. In addition to laws such as the U.S. Inflation Reduction Act, many governments plan to phase out sales of new internal combustion engine (ICE) vehicles as soon as 2030, while several manufacturers have pledged to sell only zero-emissions new cars and vans by 2040. It is a healthy trend, as BEVs are an important part of the fight against climate change.
As BEVs start to proliferate, aluminium has become the fastest-growing automotive material. Today, BEVs typically contain more than three times as much aluminium as non-BEVs for structural parts. And with good cause: aluminium-intensive BEVs are more efficient, safer, more sustainable, more durable, and perform better. Aluminium is strong, lightweight, naturally corrosion-resistant, and can be recycled over and over again.
Aluminium-intensive BEVs include the Ford F-150 Lightning, Lucid Air, Tesla Models S and X, Nio ES6 and ES8, and Jaguar I-Pace. Then there are multi-material BEVs with significant aluminium content: Tesla Models 3 and Y; Audi e-tron, the Rivian R1T; Porsche Taycan; and others. In North America, the average BEV in 2022 has 885 pounds of aluminium content, 85% more than its non-BEV counterpart and 38% more than the average 2020 BEV.
Lightweighting with aluminium changes everything
BEV batteries are heavy. Therefore, the rest of the vehicle must be as light as possible to be efficient, and to get from point A to point B without stopping too often to recharge.
Aluminium has one-third the density of steel with the same in-service strength. That means that automotive manufacturers can replace one kilogram of steel with only 600 grams of aluminium. Andreas Afseth, Technology Director for Constellium’s Auto Body Sheet business and Technical Chair of Alumobility, points out: “A 40% weight savings converts to lower energy consumption during driving, so an aluminium-intensive vehicle can have a smaller battery for the same range.” (Alternatively, it can use the same size battery for greater range.)
Lightweighting a vehicle with aluminium enables secondary weight savings for other parts, too, such as brakes and suspension systems. When a BEV weighs less, it can carry more passengers and cargo while maintaining performance.
Not only are batteries heavy, they are by far the most expensive part of a BEV. A smaller battery pack brings a vehicle’s price down dramatically. In fact, despite its reputation as being more expensive than steel, aluminium is actually quite cost competitive as a material for BEVs. This is in large part because it allows for smaller battery packs, but also because automotive manufacturers can use less of it and they pay per kilogram for the material they buy. These cost savings are compounded by lower energy use over a vehicle’s lifetime, and lower recycling costs at the end of use.
Aluminium is safer and more durable
Thanks to its energy absorption properties, aluminium is an ideal material for the Crash Management Systems (CMS), battery enclosures, and rocker panels of BEVs. And because there’s no engine in the front end of an electric vehicle, its CMS has to be particularly strong and ductile, making aluminium the obvious material choice.
In addition to being safer, aluminium BEVs are more durable, with a longer lifespan and less maintenance required. Because they are lighter, they put less stress on the brakes and suspension. And, aluminium does not rust, but forms a protective surface oxide barrier.
Aluminium is more sustainable
Aluminium is unmatched in terms of sustainability because it is recyclable without a loss in qualities, including strength, durability, and formability. Recycling aluminium uses around 5% the energy of producing primary metal, and reduces carbon emissions by as much as 95%. Automakers can further reduce their footprint (and their costs) by implementing a closed-loop process in production, using scrap from the press shop or recycled at the end of a vehicle’s life.
Constellium is currently leading a consortium of suppliers and automakers (including BMW) on a research project at its University Technology Center (UTC) at Brunel University London. Martin Jarrett is Technology Director for Constellium’s Automotive Structures & Industry business unit and leads the UTC. He says the project, called CirConAl (Circular and Constant Aluminium), is about “investigating opportunities to obtain high-levels of post-consumer aluminium, and remelt the scrap to produce high-strength aluminium alloys with ultra-low embodied CO2.” In other words, to take full advantage of aluminium’s circularity and turn “dirty” scrap into value-added vehicle parts.
There’s another reason aluminium is the most sustainable material choice: lighter BEVs with smaller battery packs require fewer battery cells and less mining for raw materials.
The door is open to aluminium for every part
Nearly every part of a vehicle can be made of aluminium. The material has seen steady growth in body-in-white, battery housings, e-motors, rockets and doors, which a 2023 Ducker Carlisle study found to be among the greatest contributors to a projected additional 100 pounds of aluminium per vehicle produced in North America. According to Afseth, “A door is 40-50% lighter in aluminium than in steel, and it’s a made on a subassembly line, so you don’t have to change all the equipment in the assembly line.”
The same study found that as the BEV market grows, so will demand for aluminium extrusions, notably for battery enclosures, which provide lightweighting opportunities along with thermal management and crash resistance. However, according to Jarrett, until now, “The market was heavily driven by quite complex aluminium structural battery enclosures that required specific capital costs. It wasn’t really sustainable.”
Since 2020, Constellium has been leading a group of automotive suppliers and manufacturers (including BMW and Volvo), in a major research project called ALIVE (Aluminium Intensive Vehicle Enclosures). Also in development at Constellium’s UTC, the project seeks to design and prototype multiple variations of structural aluminium battery enclosures in an affordable way, by using the same line for all. The consortium has already reduced capital costs by 50-60%, while developing state-of-the-art lightweight modular enclosures.
Clearly, BEVs are the vehicle of the future, while aluminium is the material helping to electrify their growth.
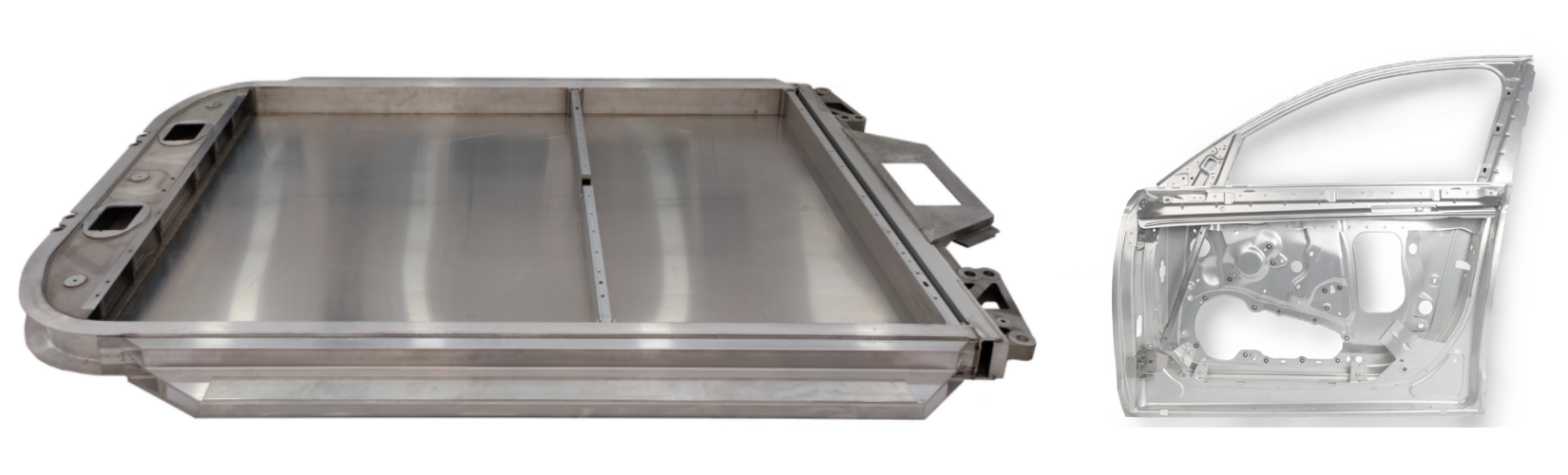
Left: Battery enclosures provide lightweighting opportunities along with thermal management and crash resistance.
Right: An aluminium door is 40-50% lighter than a steel one.
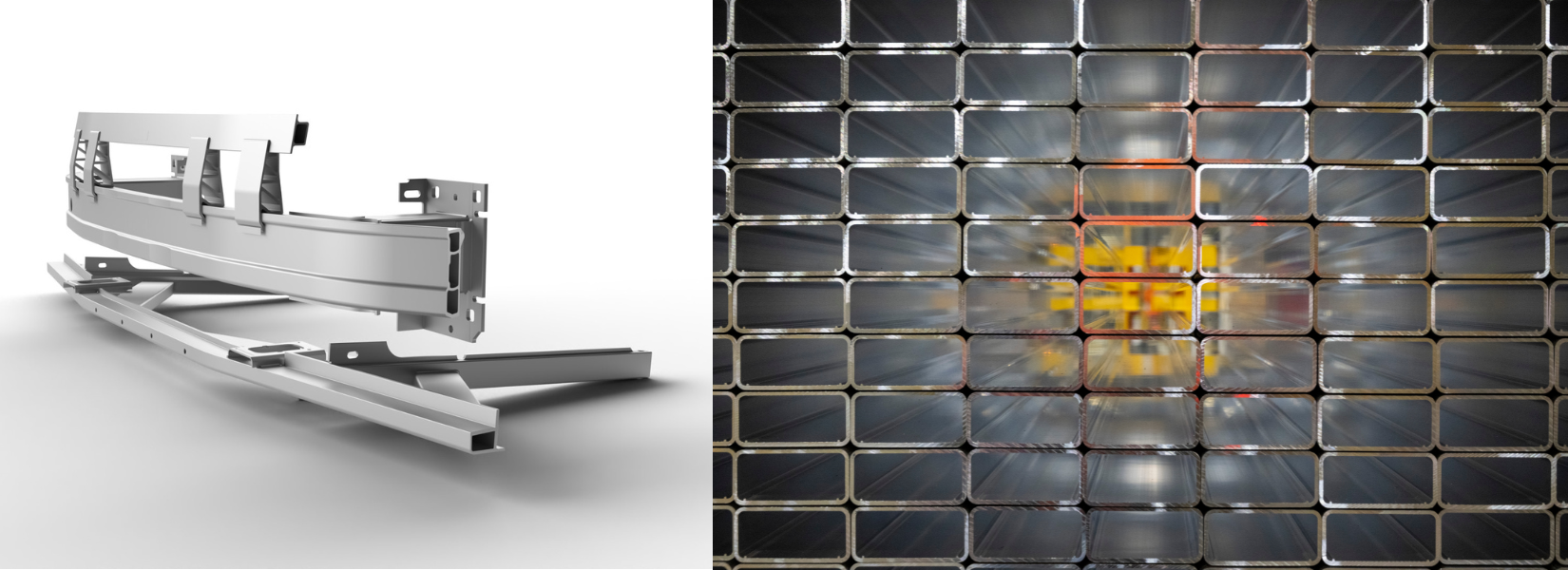
Left: The Crash Management System of an EV has to be particularly strong and ductile, making aluminium the obvious material choice.
Right: As the BEV market grows, so will demand for aluminium extrusions.
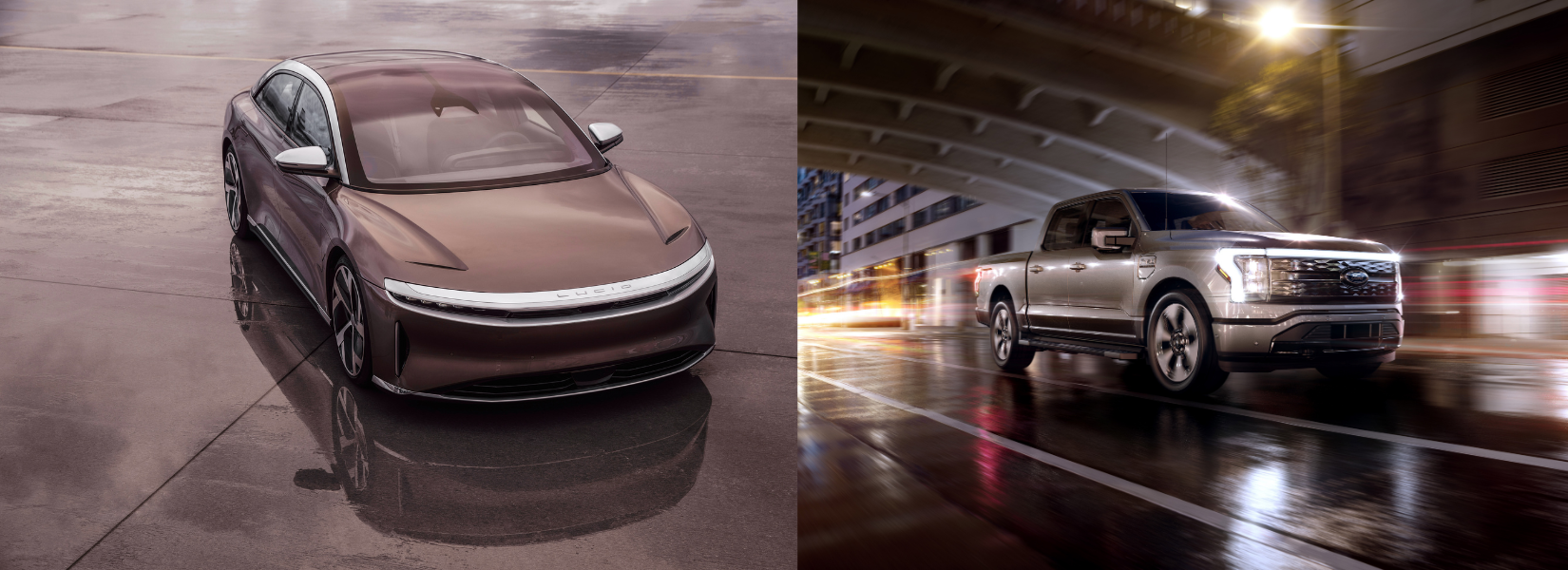
Left: The Lucid Air is an aluminium-intensive vehicle.
Right: The Ford F-150 Lightning features a military-grade aluminium alloy body.